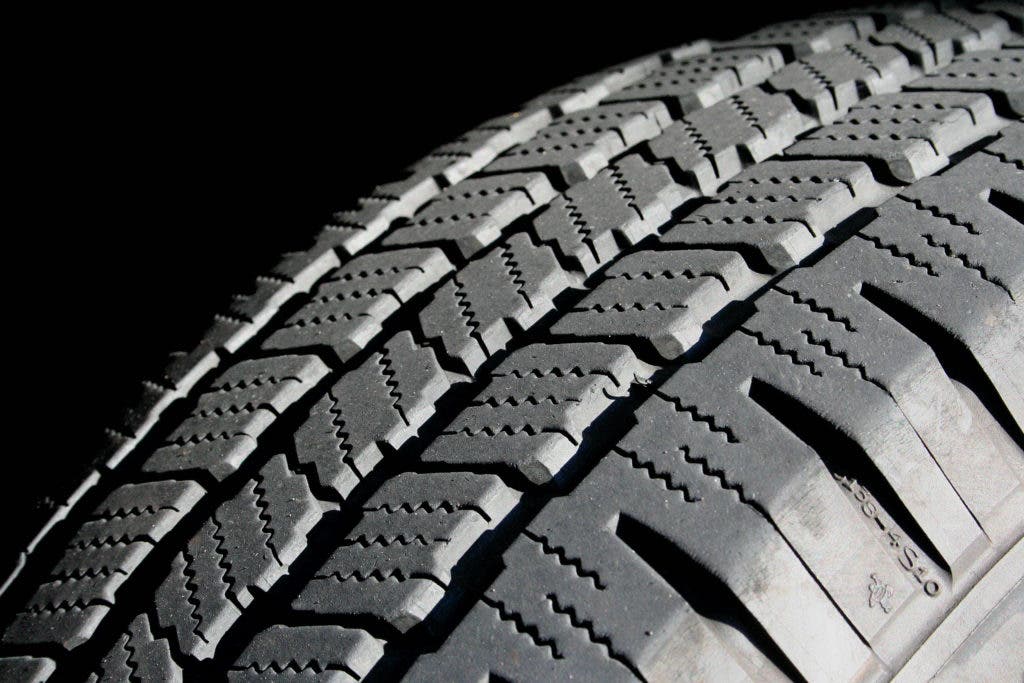
Long range electric vehicles hold the key to ridding the transport sector of petroleum liquid fuels, as long as the energy stored in the batteries comes from renewable energy sources. But even a Tesla charged from solar panels isn’t completely free of fossil fuels. Even ignoring the fossil fuel-derived energy that went in the manufacturing process, there are still plastic finishings inside the car that likely come petroleum. And even if you’d be extremely careful not to include anything fossil fuel related, you’d still hit a brick wall — the car’s tires.
Wheels of progress
Car tires are some of the most environmentally unfriendly parts in any car. These are made from natural rubber, which literally grows on trees, but also isoprene — a key molecule in any tire which is derived from petroleum through a chemical process called ‘cracking’. Developing tires from renewable materials has always been a lofty goal for scientists but despite their best efforts, this has proven extremely challenging until recently. Now, a team from the University of Minnesota claims it has perfected a three-step chemical process that can produce isoprene from renewable biomass such as trees or grasses.
Previous efforts involving the manufacturing of tires from renewable sources focused on biological processes. Specifically, researchers tried fermentation of biomass — a process similar to the one used to produce ethanol — but these attempts have failed. Isoprene proves to be a challenging molecule to generate from microbes.
The team from the Center for Sustainable Polymers at the University of Minnesota also employed microbes in their process but added new steps to produce stable isoprene molecules. Paul Dauenhauer, associate professor of chemical engineering and materials science, along with colleagues, started with sugars derived from biomass, which can include anything from corn to trees. The sugars are then fermented to create itaconic acid, which is in turn reacted with hydrogen in the presence of a metal-metal catalyst to form methyl-THF (tetrahydrofuran), an intermediate molecule key to synthesizing isoprene.

The third and final step involves converting the dehydrate methyl-THF to isoprene, and it is herein that the breakthrough lies. Another catalyst called catalyst called P-SPP (Phosphoros Self-Pillared Pentasil) and discovered at the University of Minnesota was used for this task. Remarkably, the novel catalyst had a catalytic efficiency as high as 90 percent, i.e. most of the catalytic product turns out to be isoprene.
“The performance of the new P-containing zeolite catalysts such as S-PPP was surprising,” says Dauenhauer. “This new class of solid acid catalysts exhibits dramatically improved catalytic efficiency and is the reason renewable isoprene is possible.”
“Economically bio-sourced isoprene has the potential to expand domestic production of car tires by using renewable, readily available resources instead of fossil fuels,” said Frank Bates, a world-renowned polymer expert and University of Minnesota Regents Professor of Chemical Engineering and Materials Science. “This discovery could also impact many other technologically advanced rubber-based products.”
Findings appeared in the journal ACS Catalysis.