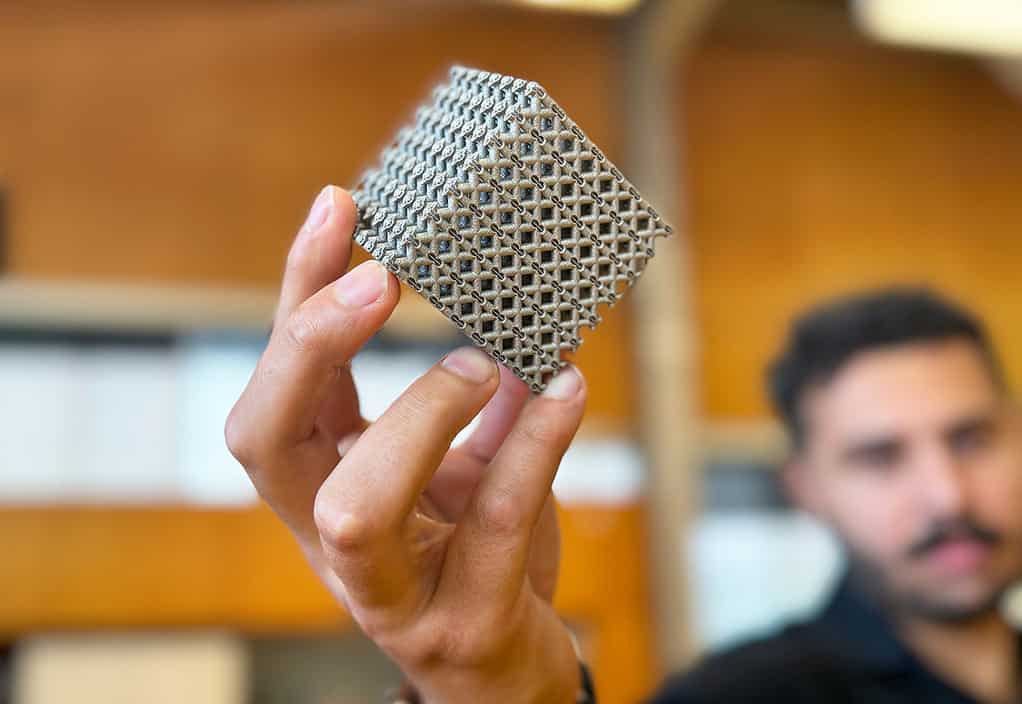
Researchers at RMIT University in Australia have made a discovery that could revolutionize manufacturing across multiple industries, from aerospace to medical implants.
The study, published in the journal Advanced Materials, introduces a titanium multi-topology metamaterial with a unique lattice structure design, offering strength-to-weight ratios previously thought unattainable in both nature and manufacturing.
This material, fabricated using advanced 3D printing technologies, boasts a strength level 50% greater than the strongest alloys of similar density currently utilized in aerospace applications.
A ‘supernatural’ material
The innovation lies in the material’s complex lattice structure, modeled after the patterns found in strong, hollow-stemmed plants and corals.
Although these cellular structures are based on nature, manufacturing issues and load stress concentration inside hollow struts have long made it challenging to replicate them in metals. This frequently resulted in early failures. The researchers have now developed a lattice structure that more evenly distributes stress throughout the material through precise metal 3D printing, greatly increasing the material’s structural efficiency and strength.
“Ideally, the stress in all complex cellular materials should be evenly spread,” said RMIT professor Ma Qian. “However, for most topologies, it is common for less than half of the material to mainly bear the compressive load, while the larger volume of material is structurally insignificant.”
The secret to manufacturing this metamaterial lies in a process known as laser powder bed fusion (LPBF). This technique involves melting layers of metal powder into precise designs using a high-powered laser beam, creating structures previously impossible to fabricate using traditional methods such as casting or machining.
The result is a titanium lattice cube that not only surpasses the strength of cast magnesium alloy WE54 but also introduces a new paradigm in the design of structural materials. The dual lattice design further contributes to its toughness by deflecting any potential cracks along the structure rather than allowing them to propagate through weak points.
“Compared with the strongest available cast magnesium alloy currently used in commercial applications requiring high strength and light weight, our titanium metamaterial with a comparable density was shown to be much stronger or less susceptible to permanent shape change under compressive loading, not to mention more feasible to manufacture,” lead author and RMIT Ph.D. candidate Jordan Noronha said.
The product’s versatility and strength open the door to a myriad of applications. From medical devices, such as bone implants that benefit from the material’s biocompatibility and strength, to aircraft and rocket components where weight reduction without sacrificing durability is paramount.
This material can withstand temperatures up to 662 degrees Fahrenheit (350 degrees Celsius). However, with further refinement, the potential for this material to withstand temperatures up to 1,112 degrees Fahrenheit (600 degrees Celsius) also hints at applications in more extreme environments, such as aerospace or firefighting drones.
Although this metamaterial has promising qualities, there may be initial obstacles to the industry’s adoption of this technology. In most production settings, the specialized manufacturing process based on LPBF is still uncommon. However, as this technology develops, more accessibility and quicker production times will most likely eventually follow.
“Traditional manufacturing processes are not practical for the fabrication of these intricate metal metamaterials, and not everyone has a laser powder bed fusion machine in their warehouse,” Noronha said.
“However, as the technology develops, it will become more accessible and the printing process will become much faster, enabling a larger audience to implement our high-strength multi-topology metamaterials in their components. Importantly, metal 3D printing allows easy net shape fabrication for real applications.”