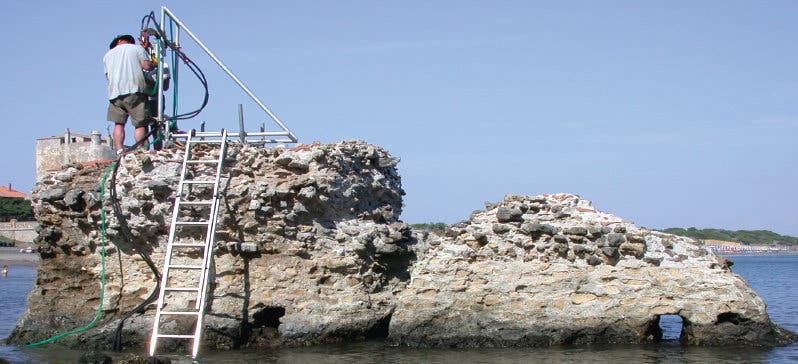
Samples from this Ancient Roman pier, Portus Cosanus in Orbetello, Italy, were studied with X-rays at Berkeley Lab. Credit: J.P. Oleson.
Almost 2,000 years ago, famed Roman historian Pliny the Elder wrote in his Naturalis Historia about the concrete poured in harbors that “as soon as it comes into contact with the waves of the sea and is submerged, becomes a single stone mass, impregnable to the waves and every day stronger.”
This insight is surprisingly spot on, according to a 2017 study that found seawater is the secret ingredient that makes Roman concrete extremely durable by encouraging the growth of rare minerals.
Concrete in some Roman piers is not only still viable today but stronger than it ever was, whereas modern marine concrete structures made from Portland cement crumble within decades.
The ancient Romans used concrete everywhere, particularly in their mega-structures like the Pantheon and Trajan’s Markets in Rome. They would make the concrete by first mixing volcanic ash with lime and seawater to make mortar, which is later incorporated into chunks of volcanic rock, the ‘aggregate’. The combination produces a so-called pozzolanic reaction, so named after the city of Pozzuoli in the Bay of Naples. Another common naturally reactive volcanic sand used for manufacturing concrete is called harena fossicia. It’s thought that Romans might have first gotten the idea for this mixture after observing naturally cemented volcanic ash deposits called tuff.
After the fall of the Roman empire, the recipe for making concrete was lost and a concrete of equal worth wasn’t re-invented until 1824 when an Englishman named Joseph Aspdin discovered Portland cement by burning finely ground chalk and clay in a kiln until the carbon dioxide was removed. It was named “Portland” cement because it resembled the high-quality building stones found in Portland, England.
The ancient Roman recipe is very different than the modern one for concrete, though. Most modern concrete is a mix of Portland cement — limestone, sandstone, ash, chalk, iron, and clay, among other ingredients, heated to form a glassy material that is finely ground — with so-called “aggregates.” These aggregates, usually sand or crushed stone, are not intended to chemically react because if they do, they can cause unwanted expansions in the concrete.
Outliving empires: Roman concrete
University of Utah geologist Marie Jackson’s interest in Roman concrete was sparked by a sabbatical year in Rome where she studied tuffs and volcanic ash deposits. One by one, she approached the factors that made architectural concrete in Rome so resilient. One such factor, she says, is that the mineral intergrowths between the aggregate and the mortar which prevent cracks from lengthening, while the surfaces of nonreactive aggregates in Portland cement only help cracks propagate farther.
While studying drilled cores of Roman harbor concrete, Jackson and colleagues found an exceptionally rare mineral, aluminous tobermorite (Al-tobermorite) in the marine mortar. The mineral’s presence surprised everyone because it is very difficult to make. For Al-tobermorite to form, you need very high temperature. “No one has produced tobermorite at 20 degrees Celsius,” she says. “Oh — except the Romans!”
Seeing how Jackon is a geologist, though, she immediately realized that the mineral must have appeared later. The team concluded with experiments backing them up that seawater percolated through the concrete in breakwaters and in piers, dissolving components of the volcanic ash and allowing new minerals to grow from the highly alkaline leached fluids, particularly Al-tobermorite and phillipsite, the latter being a related zeolite mineral formed in pumice particles and pores in the cementing matrix. In rare instances, underwater volcanoes, such as the Surtsey Volcano in Iceland, produce the same minerals found in Roman concrete.
“We’re looking at a system that’s contrary to everything one would not want in cement-based concrete,” she says. “We’re looking at a system that thrives in open chemical exchange with seawater.”
The Roman concrete samples were studied using a technique called X-ray microdiffraction at UC Berkeley Lab’s ALS. The machine produces beams focused to about 1 micron or about a hundred times smaller than what can be found in a conventional laboratory.
“We can go into the tiny natural laboratories in the concrete, map the minerals that are present, the succession of the crystals that occur, and their crystallographic properties. It’s been astounding what we’ve been able to find,” Jackson said.
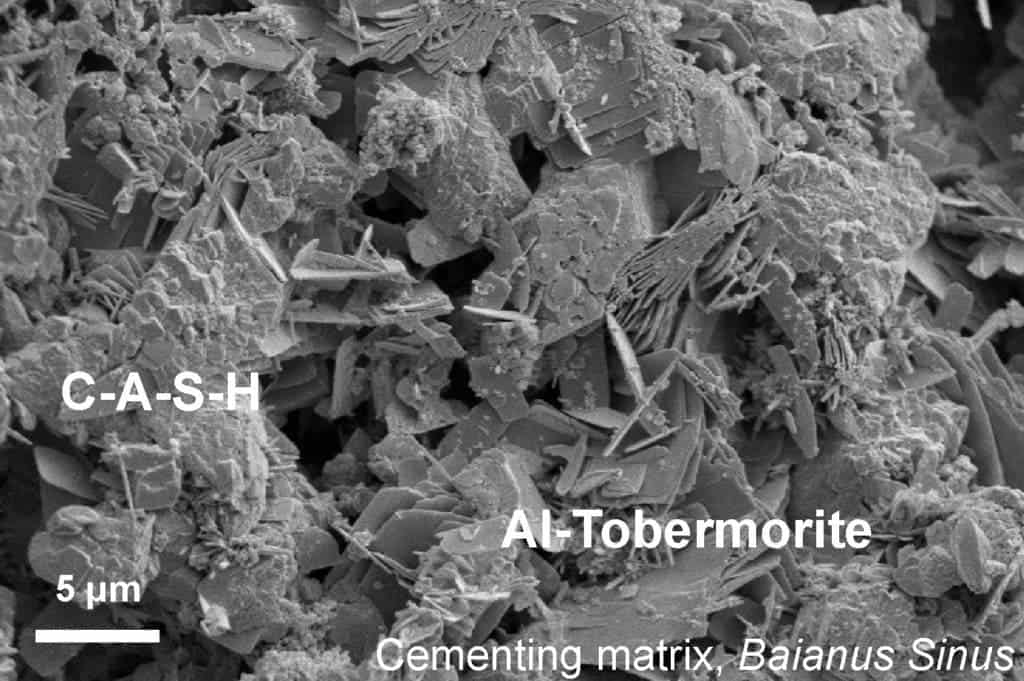
This microscopic image shows the lumpy calcium-aluminum-silicate-hydrate (C-A-S-H) binder material that forms when volcanic ash, lime, and seawater mix. Platy crystals of Al-tobermorite have grown amongst the C-A-S-H cementing matrix. Credit: Marie Jackson.
The concrete industry was valued at $50 billion in 2015 in the United States alone. That year, 80 million tons of Portland cement were made or roughly the weight of about 90 Golden Gate Bridges or 12 Hoover Dams. Given the durability of Roman concrete and the substantial carbon dioxide emissions resulting from Portland cement manufacturing, why aren’t we doing it more like the Romans?
It’s not that easy at all, says Jackson. The Romans were quite fortunate to find volcanic ash in their vicinity. Also, the ingredients for their concrete recipe can’t be adapted anywhere in the world. “They observed that volcanic ash grew cements to produce the tuff. We don’t have those rocks in a lot of the world, so there would have to be substitutions made,” Jackson said.
Additionally, Roman concrete takes time to develop strength from seawater and has less compressive strength than typical Portland cement.
Nevertheless, Jackson is closely working with colleagues to make an alternative recipe based on local materials from the western U.S., including seawater from Berkeley, California. Jackson is also leading a scientific drilling project to study the production of tobermorite and other related minerals at the Surtsey volcano in Iceland.
This kind of cement could be very useful for some niche applications. For instance, the Roman cement could be employed in a tidal lagoon project meant to harness tidal power, currently planned in Swansea, United Kingdom. To recuperate the cost incurred from building it, the lagoon would have to operate for 120 years.
“You can imagine that, with the way we build now, it would be a mass of corroding steel by that time,” Jackson said.
Unless it’s made of Roman concrete.
Meanwhile, more tests are being carried out to evaluate the long-term properties of marine structures built from volcanic rock and how these fair against steel-reinforced concrete.
“I think people don’t really know how to think about a material that doesn’t have steel reinforcement,” Jackson said.