The building sector is the single largest contributor to greenhouse gas emissions (accounting for 40% of global emissions) and a big consumer of plastics, with manufacturing processes that can pollute the air, land and water. Seeking solutions, a team of researchers have now created a rice-husk-based insulation material.
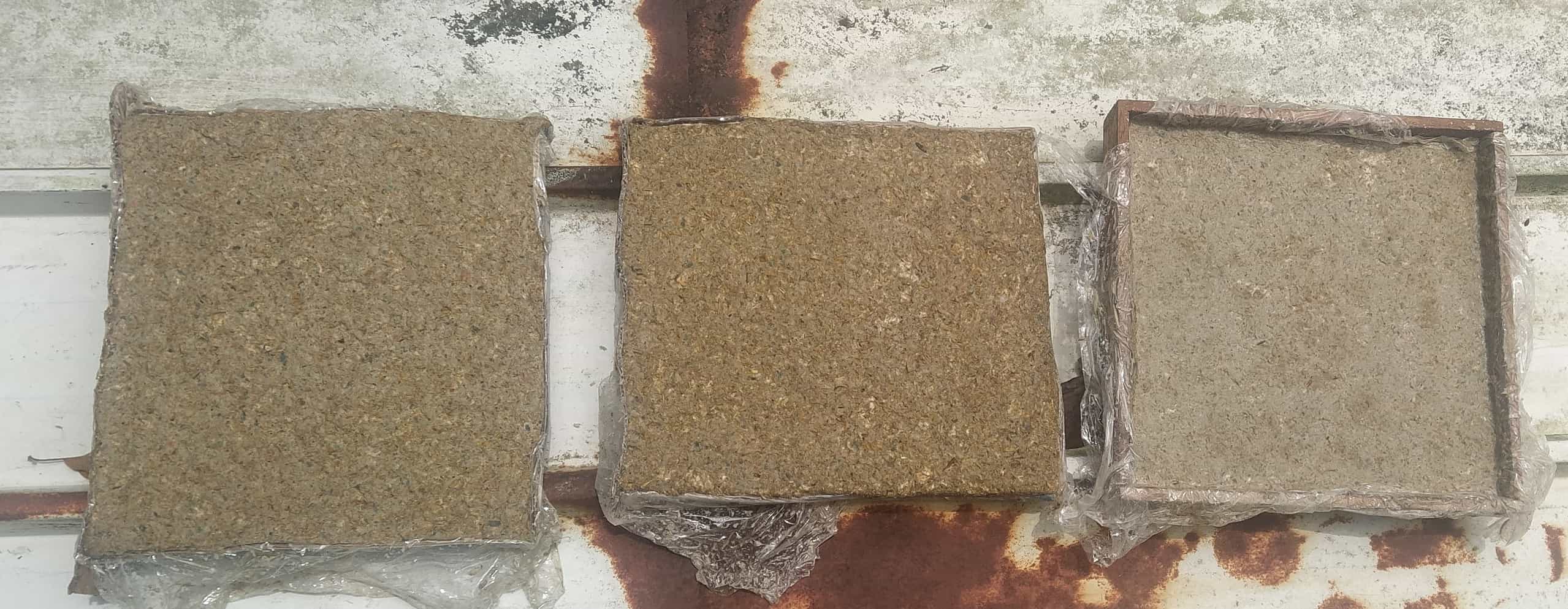
Traditional insulation materials used in building applications, such as fibreglass and rock wool, are mostly taken from petrochemical sources. In recent years, researchers have looked at agro-industrial waste as a more sustainable alternative, for example using cane fibers, coffee husks, recycled newspapers, textile fibers and sheep’s wool.
Dr. Nacarí Marín Calvo, a researcher at the Universidad Tecnológica de Panama, and her colleagues have worked on a new rice-husk-based insulation material and evaluated its thermal and mechanical properties. “It has competitive thermal conductivity compared to many natural and recycled insulation materials,” Calvo said in a news release.
A four-ingredient recipe
The study was done in rural Panama, where rice husks are considered agricultural waste — normally disposed of in landfills or incinerated. To produce the mix, the researchers shredded the husks and then added cellulose, obtained from recycled and shredded newspaper. They finally added borax, making the mix fungus resistant and fire retardant.
All the components were bonded with glue. The researchers tested different material compositions to determine the behavior of the material when more or less rice husk was used. The first mix was made from 14% newspaper, 9% rice husk, 15% borax and 62% glue. They tried two additional compositions with more rice husk and less newspaper.
“We found that the results were similar in all three compositions in k-values (thermal conductivity, the ability of a material to conduct heat), maximum stresses, and compressive strength values,” Marín Calvo said in a news release
A lower k-value means that the material is better for insulation. For the tested compositions, the k-value ranged from 0.0409-0.04607 watts per meter Kelvin (W/mK). Other natural materials have k-values ranging from 0.027 to 0.1 W/ m/K.
The researchers also tested tensile strength, which is the maximum stress that a material can withstand while being stretched or pulled before breaking. For the tested compositions, average tension ranged from 1.31 to 1.76 megapascals (MPa). Pascal is the unit used to measure the force applied at a 90° angle on the surface of an object. Materials based on cardboard, cement, and sand have similar tensile strength values.
While the results are encouraging, the researchers said more studies will be needed to confirm the material’s insulating properties and how it handles climates different from the high humidity of Panama. “We are evaluating the degradation of the developed material under ambient controlled conditions,” Marín Calvo said.
They also called for further research on other configurations, such as adding long fibers pointing in one direction to reinforce the behavior of the material in tension. “The material could also potentially be used in various engineering domains, including the production of lightweight components, construction panels, and sustainable packaging,” Marín Calvo said.
The study was published in the journal Frontiers in Built Environment.