Researchers from the U.S. have developed a new recycling method that not only makes the polyester PET longer lived, but stronger and more valuable.
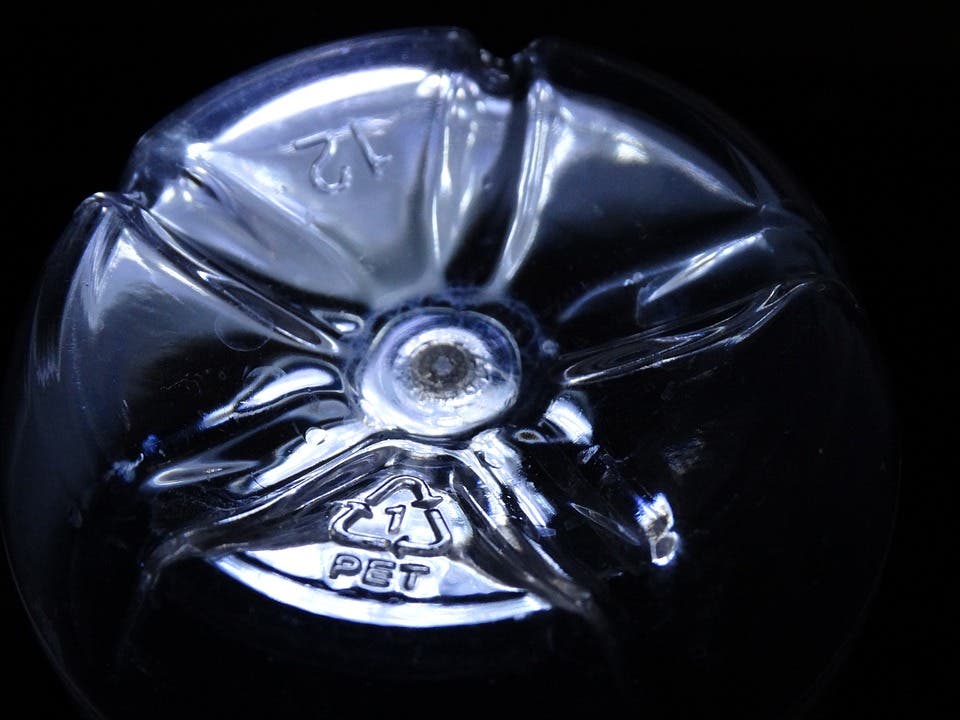
A lot of the plastic objects you use every day, from beverage bottles to clothes and carpets are made from polyethylene terephthalate (PET), a type of polyester. Like most plastics, PET is recyclable — but it also degrades during this process, the team writes. PET thus loses value over time. Another problem is that we just tend to churn out a lot of PET — roughly 26 million tons per year — and later toss is straight into the landfill and oceans. There, the roughly 80% of PET we don’t recycle wallows for a few hundred years before biodegrading completely.
One team of researchers plans to fix this by developing a recycling process that actually makes the PET better than it was initially.
Upcycling
“Standard PET recycling today is essentially ‘downcycling,'” says senior author Gregg Beckham, a Senior Research Fellow at NREL.
“The process we came up with is a way to ‘upcycle’ PET into long-lifetime, high-value composite materials like those that would be used in car parts, wind turbine blades, surfboards, or snowboards.”
Researchers at the U.S. Department of Energy’s National Renewable Energy Laboratory (NREL) are behind the new recycling process. They combined reclaimed PET with products derived from renewable material, such as waste plant biomass. Two types of fiber-reinforced plastics (FRPs) were created this way, both of which are two to three times more valuable than the original PET, the team reports.
They also predict that these composite products would require 57% less energy to manufacture than PET reclaimed through the current recycling process. It would also emit 40% fewer greenhouse gases than standard petroleum-based FRPs, which the team calls ‘significant’.
“The idea is to develop technologies that would incentivize the economics of PET reclamation,” says Beckham. “That’s the real hope—to develop ‘second-life’ upcycling technologies that make single-use waste plastic valuable to reclaim. This, in turn, could help keep waste plastic out of the world’s oceans and out of landfills.
The new materials, however, aren’t ready to leave the lab. The team plans to analyze their properties further and to determine how well the process would scale to a manufacturing setting. They also hope to develop composites that can themselves be recycled; the current ones can last years and even decades but are not necessarily recyclable afterward. They also want to develop similar technologies for other types of materials.
The findings could help protect oceans from PET waste by offering an attractive method of recycling the material.
“The scale of PET production dwarfs that of composites manufacturing, so we need many more upcycling solutions to truly make a global impact on plastics reclamation through technologies like the one proposed in the current study,” says first author Nicholas Rorrer, an engineer at NREL who also participated in the study.
The paper “Combining reclaimed PET with bio-based monomers enables plastics upcycling” has been published in the journal Joule.