New research from the U.S. Department of Energy (DOE) has designed a type of plastic that can be recycled any number of times without any loss of performance.
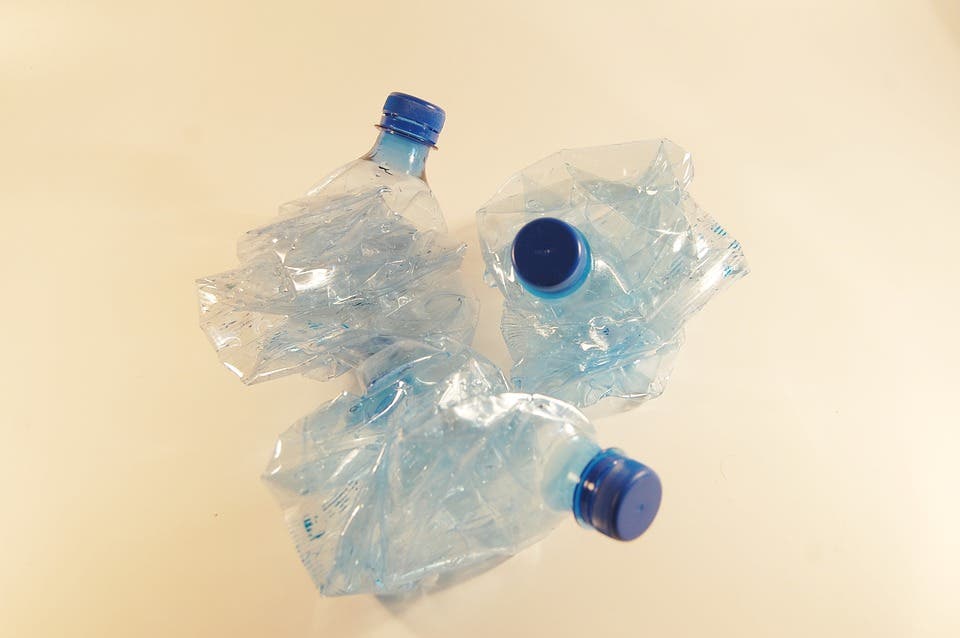
The DOE’s Lawrence Berkeley National Laboratory (Berkeley Lab) has produced a new kind of polymer that, akin to a LEGO playset, can be broken down and reassembled into a different shape, texture, and color without impairing its quality. The new material is called ‘poly(diketoenamine)’, or PDK.
Plastic with a twist
“Most plastics were never made to be recycled,” said lead author Peter Christensen, a postdoctoral researcher at Berkeley Lab’s Molecular Foundry. “But we have discovered a new way to assemble plastics that takes recycling into consideration from a molecular perspective.”
The most recyclable plastic today, PET — poly(ethylene terephthalate) — is only recycled at a rate of around 20-30%. The rest winds up in incinerators, landfills, or oceans to be burned, releasing CO2, or left to clog the Earth for a few centuries until it decomposes.
Plastics are basically long chains of carbon-based molecules (‘mers’) tied together to form polymers (‘many mers’). Their structure makes them very stable chemically, meaning they won’t rust, rot or dissolve where other materials would. In order to tailor them to particular uses, manufacturers also mix in chemical additives to improve certain properties. Fillers, for example, make a plastic tough, while plasticizers are mixed in to make it flexible. These additives are chemically-bound to individual mers, and they hold on tight. So they’re virtually impossible to remove even as plastics get processed in recycling plants. Plastics with different chemical compositions get mixed together, ground into bits, and melted during the recycling process. It’s impossible to predict the properties of the resulting material before it’s actually produced.
This tendency of recycled plastics to inherit unknown additives has prevented plastics from becoming a “circular” material — one whose original building blocks (mers) can be recovered for reuse for as long as possible, or “upcycled” to make a new, higher quality product.

Image credits Peter Christensen et al., (2019), Nat.Comms / Berkeley Lab
Christensen was part of a multidisciplinary team led by Brett Helms, a staff scientist in Berkeley Lab’s Molecular Foundry, which worked to develop a plastic that won’t have this problem.
“Circular plastics and plastics upcycling are grand challenges,” Christensen adds. “We’ve already seen the impact of plastic waste leaking into our aquatic ecosystems, and this trend is likely to be exacerbated by the increasing amounts of plastics being manufactured and the downstream pressure it places on our municipal recycling infrastructure.”
“With PDKs, the immutable bonds of conventional plastics are replaced with reversible bonds that allow the plastic to be recycled more effectively,” Helms explains.
The monomers that make PDK can be separated from any additives by simply dunking the plastic into a highly-acidic solution. The acid breaks the bonds between the monomers and the additives. This property was first discovered as Christensen was applying various acids to glassware used to make PDK adhesives, and noticed that the adhesive had changed. Christensen further analyzed the plastic with an NMR (nuclear magnetic resonance) spectroscopy instrument and found the original monomers.
Subsequent research at the Molecular Foundry showed that the acid breaks down PDK polymers into monomers while also separating them from the additive molecules. The team also showed that recovered PDK monomers can be re-cast into polymers, and that the recycled polymers don’t inherit any feature of the original material. The plastic could also be upcycled through the use of additives, such as plastifiers. The researchers believe that their new plastic could be a good alternative to many nonrecyclable plastics in use today.
“We’re at a critical point where we need to think about the infrastructure needed to modernize recycling facilities for future waste sorting and processing,” said Helms. “If these facilities were designed to recycle or upcycle PDK and related plastics, then we would be able to more effectively divert plastic from landfills and the oceans.”
“This is an exciting time to start thinking about how to design both materials and recycling facilities to enable circular plastics,” said Helms.
The researchers next plan to develop PDK plastics with a wide range of thermal and mechanical properties to use in textiles, 3D printing, and foams. They’re also looking to incorporate more plant-based compounds and other sustainable materials into the PDK plastic
The paper “Closed-loop recycling of plastics enabled by dynamic covalent diketoenamine bonds” has been published in the journal Nature Chemistry.