Despite making headlines for its environmental problems, plastic is here to stay — whether we like it or not. It’s simply too durable, cheap, and versatile to give it away soon. This also explains why it’s so ubiquitous, for better or worse. However, there’s an urgent need to change the lifecycle of this highly important material to make it more sustainable.
While some scientists are focused on cutting plastic waste, others are looking at the very source. Researchers in Canada, for instance, want to eschew traditional plastic manufacturing methods that rely on fossil fuels by tapping into one of nature’s most abundant resources: atmospheric nitrogen.
Plastic: from fossil fuels to atmospheric nitrogen
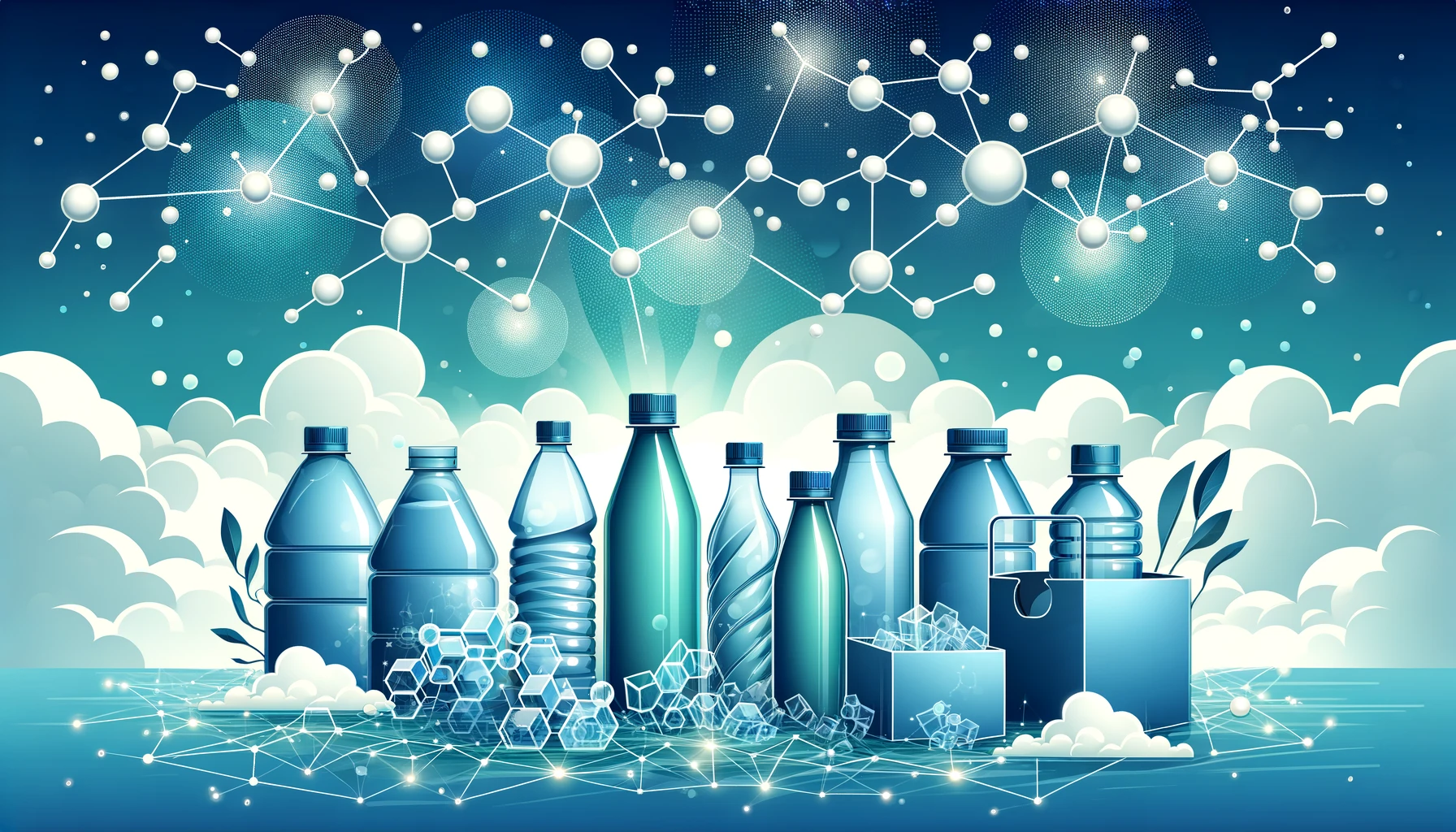
We make most of our plastic just like we did a century ago. Plastic production begins with the extraction of fossil fuels— crude petroleum and natural gas—which are then refined into basic chemicals like ethane and propane. These chemicals undergo a process called “cracking,” where high temperatures break them down into simpler compounds, notably ethylene and propylene. These compounds are the foundational building blocks or monomers for most plastics. Through polymerization, where these monomers chemically bond to form long, repeating chains, various types of plastics are synthesized.
More than 99% of all plastics come from fossil fuels. They’re made either from chemicals sourced from fossil fuels or recycled plastic that was originally synthesized from fossil fuel-derived building blocks. At the current rate of production, by 2050, greenhouse gas emissions from plastic could reach 2.8 billion tons per year. That’s as much as 615 five-hundred-megawatt coal plants.
We all know that fossil fuels are not sustainable, whether they’re burned for energy or processed into plastic. Although the timeline is fuzzy and progress is not nearly as fast as we’d like to see, the phase-out of fossil fuels is inevitable. But herein lies a problem: how would we make plastic then?
It sounds like a problem for future us that would be incredibly nice to have, considering the greatest existential threat humankind has ever faced: climate change. But it’s still a problem nevertheless, one that forward-thinking researchers at Dalhousie University are looking to tackle now.
While some alternative plastics are made from renewable bio-based materials such as starch or cellulose, Joe Bedard, a PhD candidate at Dalhousie University, has turned to an unlikely ally: our atmosphere.
Nitrogen makes up about 78% of the atmosphere, making it one of the most abundant and readily available resources in the world. It has one fatal flaw though: it is extremely unstable when condensed, which is why it is often used to make explosives. Bedard and colleagues managed to tame atmospheric nitrogen by first converting it into ammonia and then combining it with phosphorus molecules that form stable ‘cages’. It is these molecular cages that can house the nitrogen molecules, forming the foundation for a completely new class of plastic materials.
“Our primary motivation stemmed from a societal challenge – the inevitable shift away from fossil fuels. While this shift is crucial for our future, it presents a significant problem: fossil fuels are also the primary source of the building blocks of our materials, especially plastics,” Bedard told ZME Science during an interview at the Falling Walls conference in Berlin, where his research won first place at the event’s Emerging Talents category.
“We turned our focus to nitrogen, a vastly abundant component of our atmosphere, constituting about 78%. Typically, nitrogen is underutilized by humans, primarily serving as a carrier gas. Our idea was to harness this abundant resource for plastic production. However, the challenge lays in the fact that condensed nitrogen is often used for making explosives and is quite unstable.”
“We discovered a novel use for phosphorus, an element in the ‘P’ block of the periodic table, often overlooked in mainstream applications.”

These molecular cages can house multiple nitrogen molecules. They can also be linked together, forming the foundation of new plastic materials. Bedard used this method to produce plastic films and rigid pieces. The pieces can be stretched, bent, and molded in much of the same way as traditional plastics.
Interestingly, these new materials also have unique properties compared to traditional plastics. One of them is that they’re naturally flame-retardant. For instance, when exposed to fire, the plastic film chars externally without igniting. This quality makes it particularly suitable for use in environments where flame resistance is crucial, such as space exploration.
Another class of nitrogen-derived plastic that the researchers are working on is biodegradable. If discarded in the right environment, the plastic will decompose into its components: nitrates and phosphates, which are incidentally fertilizers. “We need to look at the impacts of that and how we can control if there are ways we can control how it degrades more effectively,” Bedard added.
An intriguing direction of research involves adding small quantities of these alternative plastics to other materials to enhance their strength. This is akin to adding rebar to concrete for reinforcement. This approach is still in the early stages but shows great promise.
Other properties and applications are waiting to be discovered thanks to the high flexibility of the nitrogen-derived polymer.
“We’ve done a lot of testing about what the material properties of these things are. One advantage is that there are so many different ways you can make these plastics that are available to us as chemists — we barely scratched the surface.”
“You can make them hard or very brittle; you can make them stretch or deform them and they will retain their shape.”
“We have yet to really see where we can go with this.”
Basics to applications
Bedard, who has a background in polymer and inorganic chemistry, emphasizes that it all started as fundamental research. It was only later that Bedard and his supervisor Dr. Saurabh Chitnis, who initially dreamed up the project, were awed by the potential practical applications.
“No one had ever made anything like this. I spent a lot of time looking at all the data and trying to figure out if I had what I thought I had.”
“Then there was a moment — I guess you can call it a eureka moment — when I realized almost by accident that the thing I was making could become plastic. I rushed to my supervisor, like they show in the movies, and I told him ‘Oh my God, we have it!’
“When I first made the plastic, I wasn’t expecting it to be what it was. I was expecting it to be kind of brittle, like something you could snap with your fingers. And it wasn’t like that at all.”
Despite the many promising features of nitrogen-based plastics, challenges remain. The material is highly viscous during mixing, which means you need a lot of energy to stir the solution. Scaling up manufacturing to industrial standards requires somehow extracting nitrogen from the air and converting it into ammonia in a way that is both efficient and environmentally friendly.
The researchers are now looking to partner up with local green nitrogen facilities in Nova Scotia. This will enable them to explore how this entire process can be scaled.
The research was published in the Journal of the American Chemical Society.