Researchers at ETH Zürich have developed the first 3D-printing method that can produce highly-complex, porous glass objects. The approach relies on a special resin that can be cured using ultraviolet (UV) light.
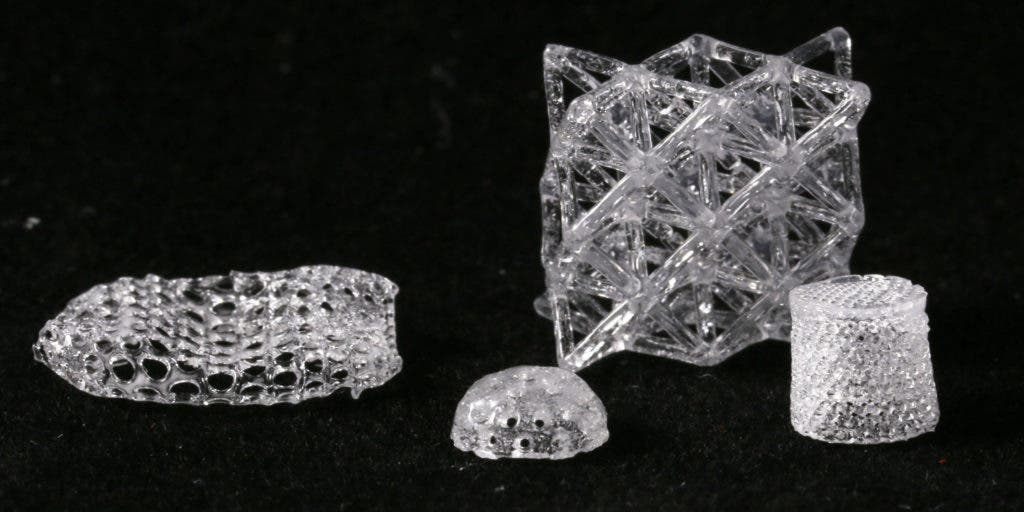
Image credits Group for Complex Materials / ETH Zurich.
Glass has been a long-standing goal of 3D-printing enthusiasts for a long time now; it’s also proven to be the most elusive. The inherent problem regarding printable glass is that the material requires very high temperatures to process. The two approaches we’ve tried so far are to either ‘print’ molten glass — which requires expensive and specialized heat-resistant equipment — or to use ceramic powders as ink to sinter into glass — an approach that sacrifices precision and thus the complexity of the finished product.
In order to solve the issue, the team from ETH Zurich went back to the roots, and worked from stereolithography, one of the first 3-D printing techniques developed during the 1980s. They developed a resin which contains a plastic material and organic molecules tied to glass precursors that can be hardened by exposure to UV light.
A light touch
When blasted with UV light — the team says commercially available Digital Light Processing technology works just fine — photosensitive components in the resin bind together. The plastic in the ink forms into a maze-like polymer that provides the structural framework. Ceramic-bearing molecules link together in the empty areas created by the framework.
This allows an object to be built layer-by-layer, and by modifying the intensity of the UV light, the team can change various parameters in each layer. Weak light intensity results in large pores, for example, while intense illumination produces small pores.
“We discovered that by accident, but we can use this to directly influence the pore size of the printed object,” says Kunal Masania, a co-author of the study.
So where does the glass fit into this? The team explains that they can modify the microstructure of their (hardened) ink by mixing silica with borate or phosphate and adding it to the resin. Silica is the main component of glass, while borate and phosphate are added to specialized, heat-resistant and optical glass respectively. The team explains that their approach allows for single or multiple types of inks to be mixed into a single object, allowing for several kinds of glass to be produced in the end.
The final step involves using heat to actually turn the hardened ink into glass. The printed ‘blanks’ are fired at 600˚C, which burns away the polymer framework, and then at 1000˚C to transform the ceramic structure into glass. During the thermal treatment, the blanks shrink significantly, the authors report, while becoming as transparent and hard as window glass.
So far, the approach can only be used for small objects — about the size of a die. Larger objects such as bottles, drinking glasses, or window panes cannot be produced this way, but that wasn’t the goal here, Masania explains. The team wanted to prove that glass is a viable material for 3D-printing, he explains.
The team has applied for a patent on their technology and are negotiating with industry representatives to take their process to market.
The paper “Three-dimensional printing of multicomponent glasses using phase-separating resins” has been published in the journal Nature Materials.