Researchers are now one step closer to developing super-strong composite materials, thanks to the mantis shrimp – a marine crustacean strong enough to cut a finger.
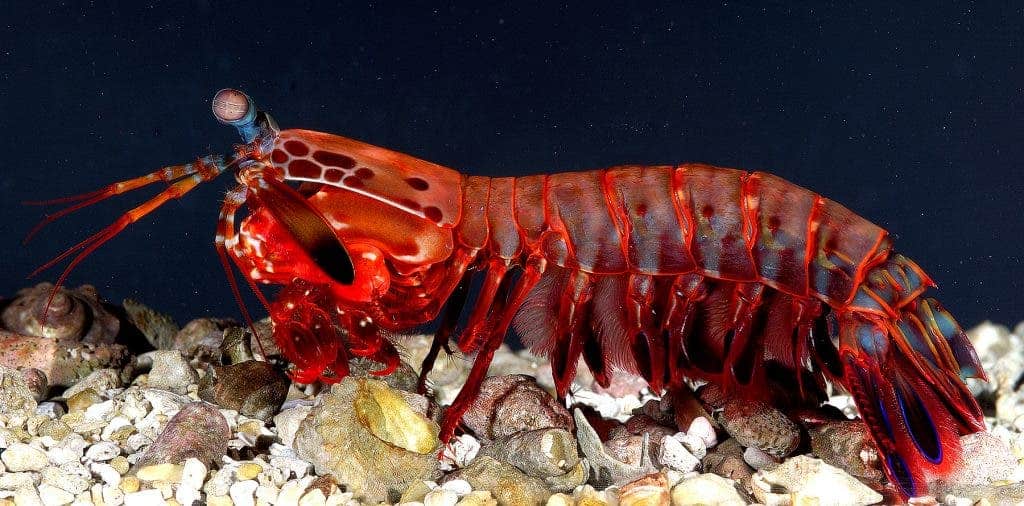
The mantis shrimp is an impressive creature and generally speaking, they come in two varieties: the “crushers” and the “spearers”. The first category crushes the shells of its prey using a fist-like appendage called a dactyl club. Its crushing ability is so strong that at least one man has had a finger amputated after a mantis shrimp strike. David Kisailus, the Winston Chung Professor in Energy Innovation in UCR’s Bourns College of Engineering, and his team have been studying this variety of the multicolored marine creature to see how it managed to pull such a strong force without hurting itself.
According to their latest study, published in the journal Advanced Materials, mantis shrimp use a unique herringbone structure, not previously reported in nature, within the appendage’s outer layer. This very tough herringbone structure allows the shrimp to not only inflict terrible damage to the prey, but also protect their own structure during impact.

“The smasher mantis shrimp has evolved this exceptionally strong and impact-resistant dactyl club for one primary purpose—to be able to eat. However, the more we learn about this tiny creature and it’s multi-layered structural designs, the more we realize how much it can help us as we design better planes, cars, sports equipment and armor”, Kisailus said.
The dactyl club can reach an acceleration of 10,000g, unleashing a barrage of impacts with the speed of a .22 caliber bullet. When viewed under a microscope, the structure features fibers of chitin and calcium compounds are arranged in a series of sinusoidal waves, resulting in the herringbone pattern. When a the crushing takes place, the huge force exerted by the structure (and conversely, on the structure) is dispersed through the pattern and the mantis shrimp is protected. Nicholas Yaraghi, a graduate student in Kisailus’ group who led the current research said that this is the first time this type of interaction was observed in nature.
“We knew from previous studies that the impact region allows the mantis shrimp to transfer incredible momentum to its prey while resisting fracture, but it was exciting to reveal through our research that the properties of this highly impact-resistant material are created by the novel herringbone structure,” he said.

Credit: UC Riverside
We still don’t know exactly how this structure evolved and came to be, but that doesn’t mean we can’t learn from it.
Pablo Zavattieri, Associate Professor of Civil Engineering and University Faculty Scholar at Purdue University, and his team built computational models that replicate the local details of the herringbone structure. These models indicate how the stress gets evenly distributed, mitigating the damage and preventing potential failure. Then, they 3D-printed materials in a similar structure and tested to see if they can replicate the results. The results were surprising.
“While the computational modeling results gave us compelling confirmation of the redistribution of stresses in these structures, the “wow” moment came when we tested our 3D printing samples,” Guarín-Zapata said.
They found that simply replicating the herringbone structure provides much more resistance to materials, and this technology could be used to great success when strong materials are needed.
“The smasher mantis shrimp has evolved this exceptionally strong and impact-resistant dactyl club for one primary purpose–to be able to eat. However, the more we learn about this tiny creature and it’s multi-layered structural designs, the more we realize how much it can help us as we design better planes, cars, sports equipment and armor,” Kisailus said.
They are now experimenting with more 3D-printed materials, to see how the process can be made more effective and simple.
“By using 3D printing techniques like those used by Zavattieri’s team, we can actually take what we’ve learned about the architecture of the dactyl club and manufacture new composites with traditional engineering materials like polymers and carbon fiber,” Kisailus said.
Journal Reference: Nicholas A. Yaraghi, Nicolás Guarín-Zapata, Lessa K. Grunenfelder, Eric Hintsala, Sanjit Bhowmick, Jon M. Hiller, Mark Betts, Edward L. Principe, Jae-Young Jung, Leigh Sheppard, Richard Wuhrer, Joanna McKittrick, Pablo D. Zavattieri, David Kisailus. A Sinusoidally Architected Helicoidal Biocomposite. Advanced Materials, 2016; DOI:10.1002/adma.201600786