New research at the University of Colorado Boulder (UCB) aims to pave the way to living, breathing buildings by mixing concrete with bacteria.

Image credits UCB College of Engineering & Applied Science.
Walls that heal, scrub the air clean, or even glow on demand — that’s what the team envisions for the future. Led by engineer Wil Srubar from the UCB, they’re trying to make it happen by mixing living bacteria with sand and gelatin and then having them produce concrete on the spot, out of thin air. In addition, such an approach would help scrub CO2 out of the atmosphere.
Tiny building blocks
“We already use biological materials in our buildings, like wood, but those materials are no longer alive” said Srubar, an assistant professor in the Department of Civil, Environmental and Architectural Engineering at the UCB.
“We’re asking: Why can’t we keep them alive and have that biology do something beneficial, too?”
The bacteria-laden material isn’t commercially available just yet. However, the little bugs have survived in the hardened mixture for several weeks, suggesting that the approach is viable.

Image credits Chelsea M. Heveran et al., (2020), Matter.
Srubar and colleagues experimented with cyanobacteria belonging to the genus Synechococcus. Under the right conditions, these green microbes absorb carbon dioxide gas to help them grow and make calcium carbonate—the main ingredient in limestone and, it turns out, cement. The researchers bred colonies of these cyanobacteria and injected them into the sand and gelatin matrix, which serves to provide the shape and other materials required for the desired piece of concrete.
With the right tweaks, the calcium carbonate mineralizes with the gelatin that binds the grains of sand together, producing a brick.
“It’s a lot like making rice crispy treats where you toughen the marshmallow by adding little bits of hard particles,” Srubar said.
The material effectively acts as carbon storage, because it scrubs the gas from the air and chemically binds it into a stable compound. Because the bacteria don’t die off after crystallization, they could be used to repair any cracks or similar damage sustained by the brick (or a whole building), much like the living cells in our bones. The team managed to keep around 9-14% of the bacterial colonies in their material alive for 30 days, having spent three different generations in brick form.
“We know that bacteria grow at an exponential rate,” Srubar said. “That’s different than how we, say, 3-D-print a block or cast a brick. If we can grow our materials biologically, then we can manufacture at an exponential scale.”
But are they any good as far as bricks go? It seems so — the team found that the bacteria-laden bricks have similar strength to Portland cement-based mortars humidity conditions. In the future, they see their material as being delivered in bags on-site, where it would just be mixed with water and shaped, then allowed to develop.
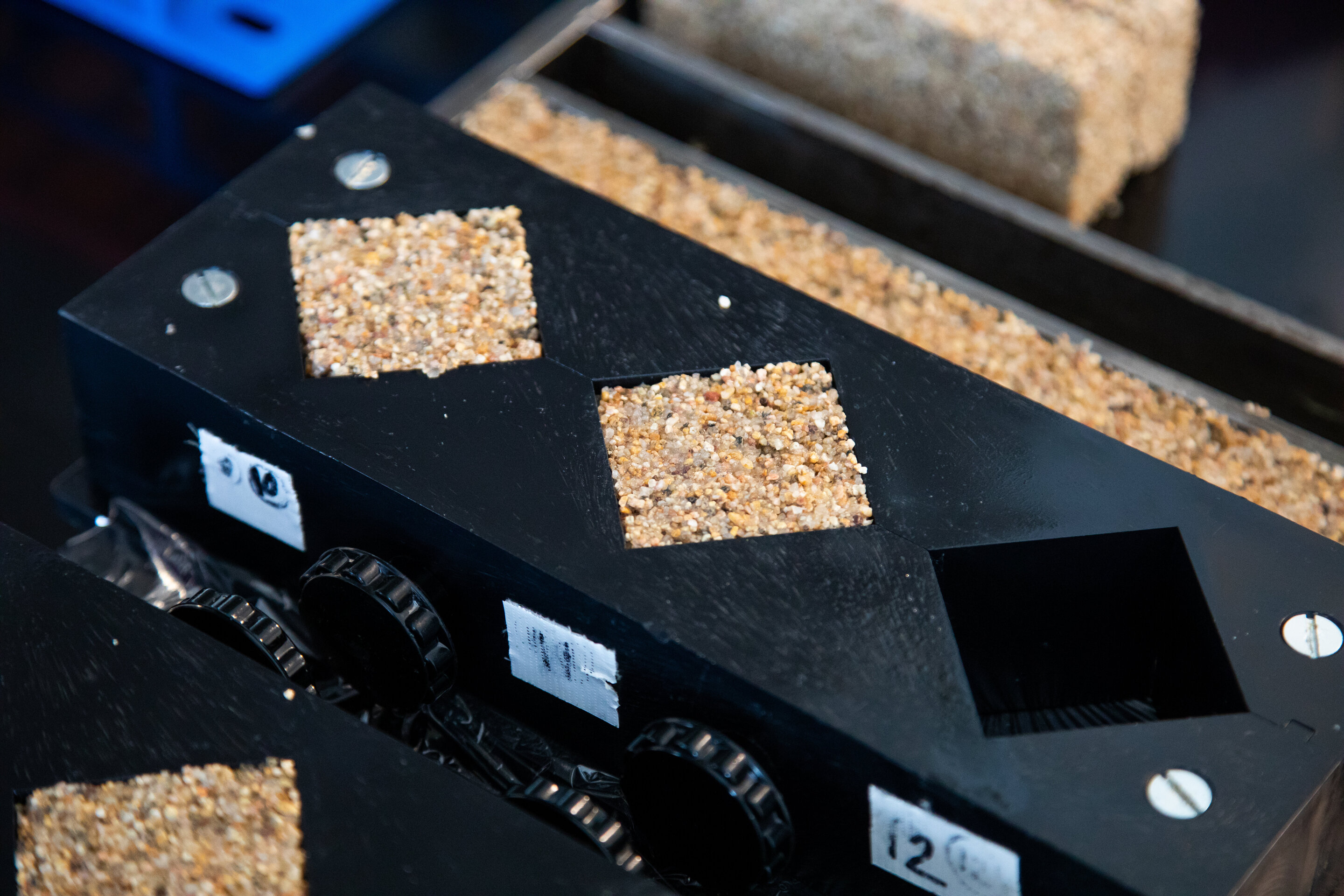
Image credits UCB College of Engineering & Applied Science.
The team also hopes to help slash emissions and energy use related to construction material manufacturing. Cement and concrete production for roads, bridges, skyscrapers and other structures generates nearly 6% of the world’s annual emissions of carbon dioxide, they explain.
However, there is still a lot of work to be done before such material becomes commercially available. One of the team’s goals right now is to grow cyanobacteria that is more resistant to dry conditions (the team’s bacteria currently need humid conditions to survive) so that they can be employed in hotter, drier areas.
The paper “Biomineralization and Successive Regeneration of Engineered Living Building Materials” has been published in the journal Matter.