Additive manufacturing, commonly known as 3D printing, has revolutionized the way we create products. The method works by creating a physical object, usually from a type of plastic or resin. But in the new study, researchers demonstrated the same method — but with metal.
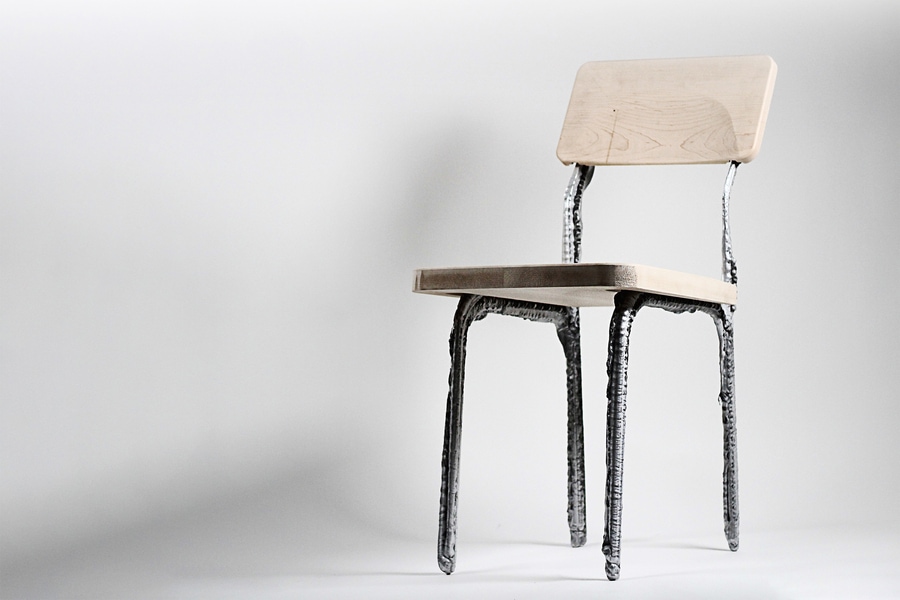
3D printing offers flexibility and efficiency compared to traditional manufacturing methods. It works like this. You have a “3D printer” that follows a digital file, adding layers of material on top of each other to build the object’s shape. Each layer is a thinly sliced, horizontal cross-section of the eventual object, which solidifies upon deposition, gradually creating the final three-dimensional product. This process allows for complex designs and shapes that would be difficult or impossible to achieve with traditional manufacturing methods.
But it is usually limited in the type of materials that you can use.
This is where Liquid Metal Printing (LMP) comes in. The novel approach was developed by researchers at the Massachusetts Institute of Technology (MIT). LMP addresses the limitations of traditional metal printing techniques by offering a faster, more scalable, and cost-effective solution. This groundbreaking technology has the potential to transform the landscape of manufacturing, making metal printing accessible for larger projects and a wider range of applications.
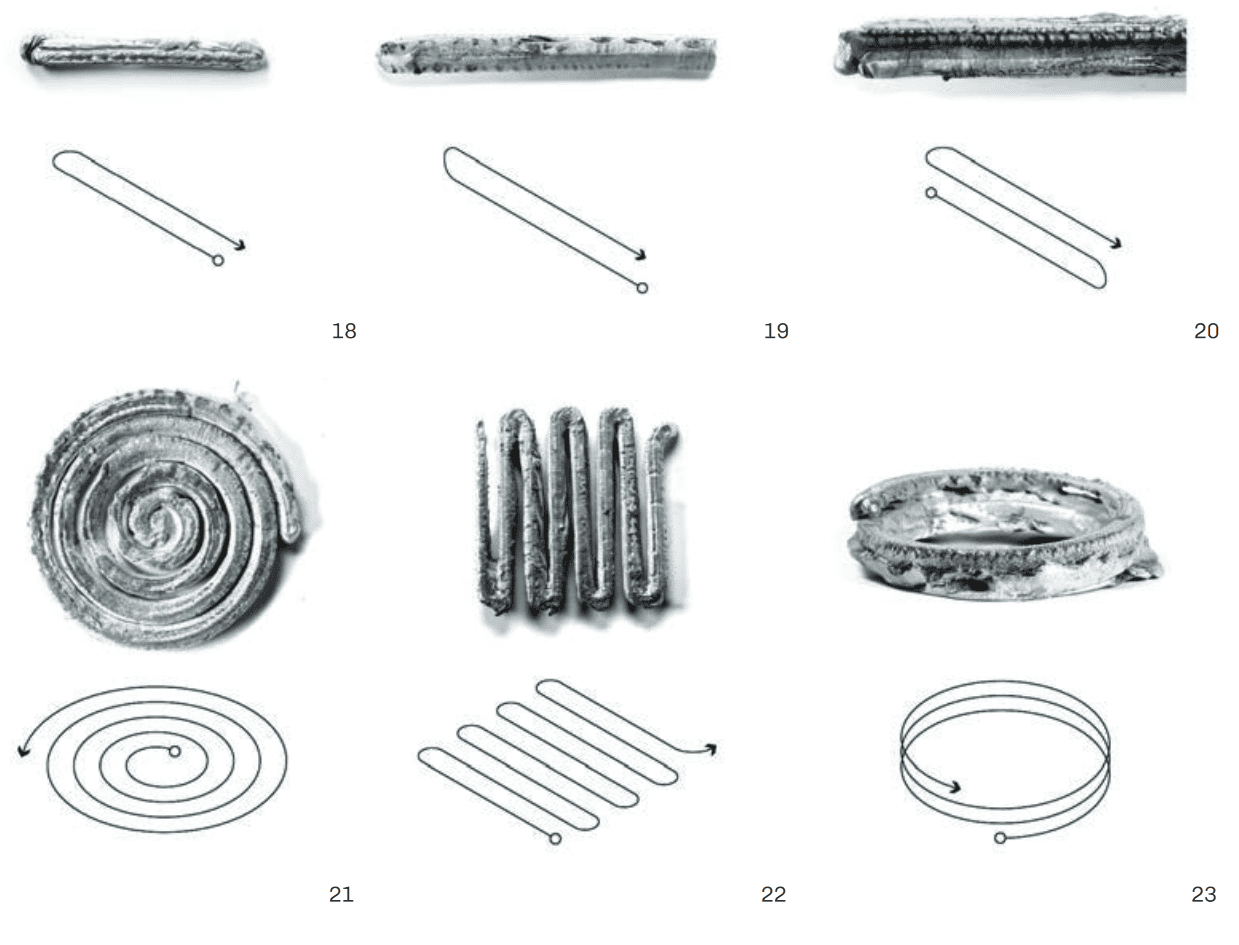
The technique also works with recycled aluminum, which further promotes sustainability. Overall, this process represents a significant shift in metal additive manufacturing, opening up new possibilities for creating large-scale metal parts more sustainably and affordably.
The process is fast and cost-effective. It can be used in architecture and industrial design, but probably not for objects that require a lot of finesse.
The reason is that there are significant limitations to this approach too.
The biggest drawback is resolution. The technique sacrifices resolution for speed. You can’t create fine details with this type of 3D printing.
“This is a completely different direction in how we think about metal manufacturing that has some huge advantages. It has downsides, too. But most of our built world — the things around us like tables, chairs, and buildings — doesn’t need extremely high resolution. Speed and scale, and also repeatability and energy consumption, are all important metrics,” says Skylar Tibbits, associate professor in the Department of Architecture and co-director of the Self-Assembly Lab, who is senior author of a paper introducing LMP.
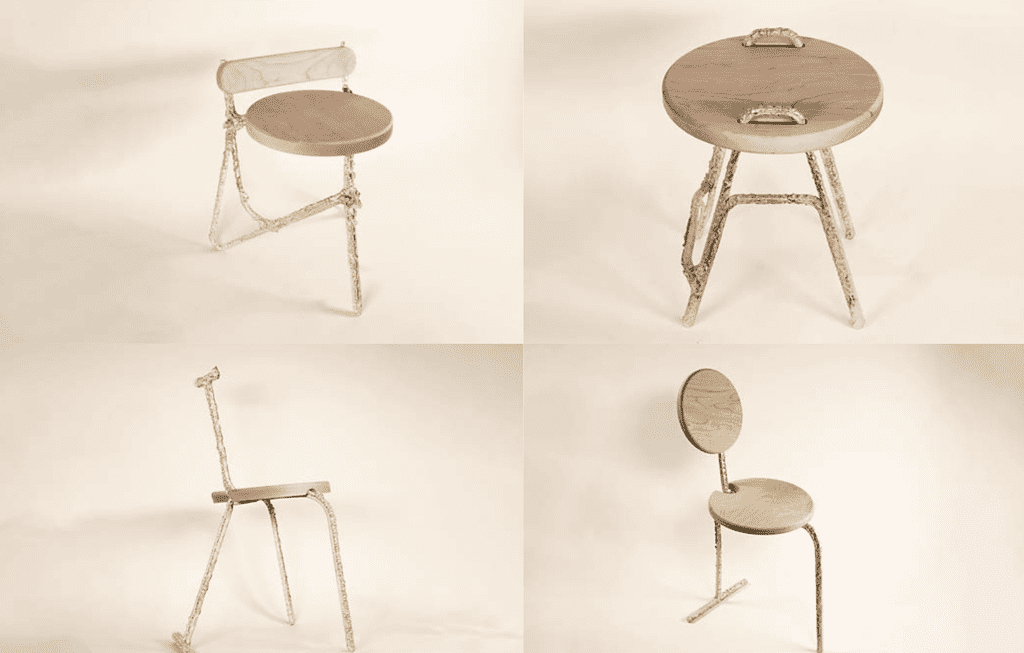
There are also technical difficulties with the technique. For instance, the material sometimes sticks to the nozzle — but if they use a larger nozzle, the quality and resolution of the print also declines.
Overall, the technique is not reliable enough to hit the market, but researchers say it’s going in that direction.
“If we could make this machine something that people could actually use to melt down recycled aluminum and print parts, that would be a game-changer in metal manufacturing. Right now, it is not reliable enough to do that, but that’s the goal,” Tibbits says.
You can read the paper presenting the technique here.