People add custom-made insoles to their footwear for many different reasons – from pain relief to foot problems to athletes wanting to improve their performance. To get the right insole, specialists need to create a profile of the feet, which means walking barefoot on mats to leave footprints. This can take a lot of time and is done in a confined space.
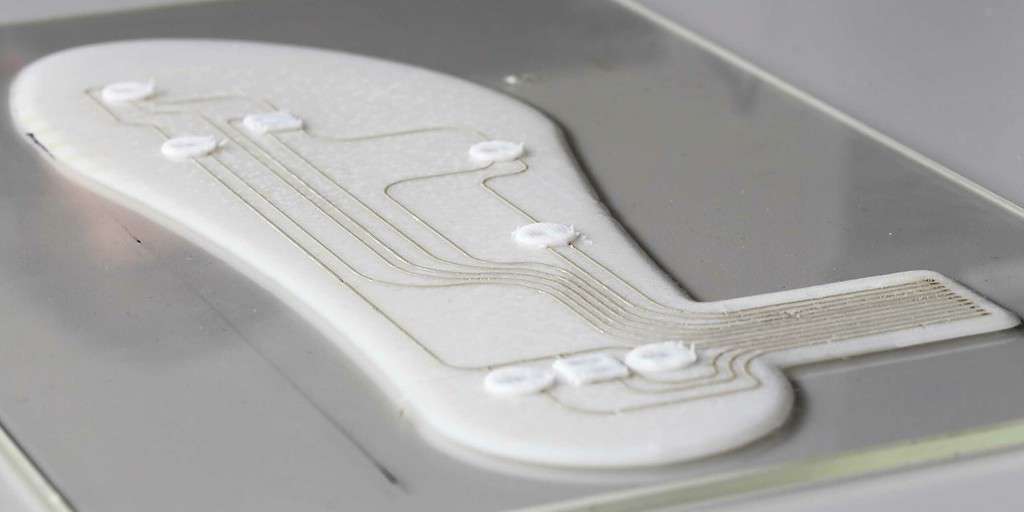
Now, Swiss researchers from the Federal Institute of Technology, the Federal Institute of Technology Lausanne and the Federal Laboratories for Materials Science and Technology found a way to improve things. They used 3D printing to produce an insole with pressure sensors that measure the pressure on the sole of the foot in the shoe.
“You can tell from the pressure patterns detected whether someone is walking, running, climbing stairs, or even carrying a heavy load on their back – in which case the pressure shifts more to the heel,” co-project leader Gilberto Siqueira, said in a statement. The invention was recently described in the journal Scientific Reports.
A new type of insole
The insoles are easy to use and easy to make, the researchers said. They are done in one single step, including the sensors and conductors, by using a 3D printer called extruder. For printing, they used several types of inks created specifically for this application. For the basis of the insole, they used silicone and cellulose nanoparticles.
They printed the conductors on the first layer using conductive ink with silver. Then they printed the sensors on the conductors in individual places, using ink with carbon black. The sensors are placed exactly where the sole pressure is greatest. To protect the sensors and the conductors, they coated them with an additional layer of silicone.
These are a lot of layers, which led to the researchers having some difficulties achieving good adhesion. However, they were able to solve this by treating the surface of the silicone layers with hot plasma. As part of their design process, they also created an interface directly inside the sole for reading out the generated data for each user.
Companies and other researchers have also worked with different concepts for insoles over the years. However, they have all relied on conventional manufacturing workflows that “cannot meet the increasing demand for digitalization and personalization,” the researchers said, a gap they believe is filled with 3D printing.
In fact, tests showed that the newly-created insole works well. “With data analysis, we can actually identify different activities based on which sensors responded and how strong that response was,” Siqueira said. But there’s work yet to be done. The insole uses a cable connection to read the data, which they hope to instead make wireless.
The researchers believe 3D-printed insoles with integrated sensors could one day be used by athletes to measure training or in physiotherapy to measure progress. Training plans could be adjusted based on the measurement data. The team has not taken any steps towards commercialization yet but they believe there’s strong market potential.