Fewer materials in nature rival the toughness and resilience of a tooth or a seashell, and it’s all due to their unique structure; viewed under powerful enough microscope, they reveal layers upon layers of micro-plates, perfectly aligned and fused together. Material scientists have long sought to produce something that imitates these structures, with comparable properties and complexity, but apart from nacre (mother-of-pearl) they’ve had very little success.
That is, not until now. A group of researchers headed by André Studart, Professor of Complex Materials at the Swiss Federal Institute of Technology in Zurich (ETH), has developed a new method that allows them to imitate the natural model almost perfectly. The team was the first to create a complex piece out of the multiple layers of oriented micro-plates that teeth and shells use.
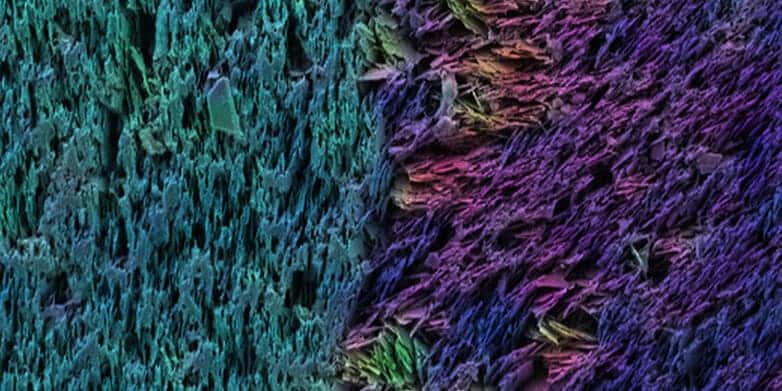
Image credits: Hortense Le Ferrand/ETH Zürich
Line them up then stack them down
They christened their method the magnetically assisted slip casting (MASC) method.
“The wonderful thing about our new procedure is that it builds on a 100-year-old technique and combines it with modern material research,” says Studart’s doctoral student Tobias Niebel, co-author of a study just published in the specialist journal Nature Materials.
The main difficulty of producing an enamel-like material lies in aligning the individual layers of micro-plates to different orientations. But the team came up with a plan, a plan so cunning you could pin a tail on it and call it a weasel: the process uses a plaster cast that the researchers created to serve as a mold into which they pour a suspension of magnetized ceramic micro-plates, such as aluminium oxide micro-plates. The plaster mold is full of pores that absorb the liquid from the suspension, solidifying the material from the outside in. During the casting, the ETH team subjects the mold and plates to a strong magnetic field, under which they act like little compass points, aligning perfectly. The field’s orientation is changed at regular intervals, moving the plates still in suspension, leaving the ones that have already solidified undisturbed.
Through the composition of the suspension and the direction of the platelets, a continuous process can be used to produce multiple layers with differing material properties in a single object. This creates complex materials that are almost perfect imitations of their natural models, such as nacre or tooth enamel.
“Our technique is similar to 3D printing, but 10 times faster and much more cost-effective,” says Florian Bouville, a post-doc with Studart and co-lead author of the study.
Utilizing the MASC method, they produced an artificial tooth with a microstructure mimicking that of a real tooth. The outer layers, corresponding to enamel, are hard and structurally complex, with deeper layers being more tough, just like dentine. The first suspension, used for enamel, contained glass nanoparticles and the aluminium oxide plates were aligned perpendicular to the surface. After it hardened, a second suspension was poured. It contained no glass, and the plates were aligned horizontally to the surface of the tooth. The tooth was then cooked at 1,600 degrees to compact and harden the material — a process known as sintering. The last step involved filling any pores that remained with a synthetic monomer used in dentistry, which polymerizes after treatment.
I can’t believe it’s not butter a tooth
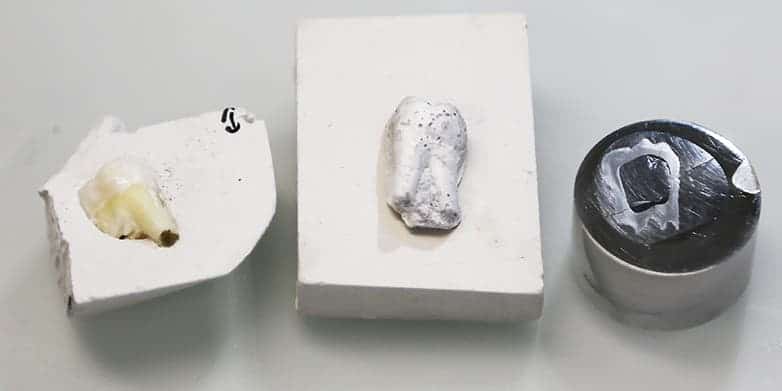
Image credits: Tobias Niebel/ETH Zurich
“The profile of hardness and toughness obtained from the artificial tooth corresponds exactly with that of a natural tooth,” says a pleased Studart.
The procedure and the resulting material lend themselves well to applications in dentistry. However, as Studart points out, the technology is still at an early proof-of-concept stage, and the study was just meant to show that the natural structure of teeth can be reproduced in a laboratory. Further refining and improving is required to make the most out of their work.
“The appearance of the material has to be significantly improved before it can be used for dental prostheses.”
Nonetheless, the finished tooth shows that a degree of control over the microstructure of a composite material can be achieved to a level which was previously only seen in living organisms. One part of the MASC process, the magnetisation and orientation of the ceramic platelets, has already been patented.
However, the new production process for such complex biomimetic materials also has other potential applications. For instance, copper platelets could be used in place of aluminium oxide platelets, which would allow the use of such materials in electronics.
“The base substances and the orientation of the platelets can be combined as required, which rapidly and easily makes a wide range of different material types with varying properties feasible,” Studart concludes.
The full paper is available on Nature.com.